新聞類別
產(chǎn)品列表
聯(lián)系我們
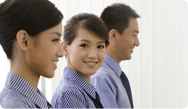
無錫市興峰機器有限公司
地 址 :無錫市新區(qū)坊前新風(fēng)路36號
電 話 :0510-88273229
傳 真 :0510-88271450
聯(lián)系人:馬總
手 機 :13806182809
郵 箱 :xf@xfjq.com
網(wǎng) 址 :www.xfjq.com
常用的六種鑄造方法及其優(yōu)缺點
發(fā)布時間:2020-04-23
鑄造是人類掌握比較早的一種金屬熱加工工藝,已有約6000年的歷史。中國約在公元前1700~前1000年之間已進入青銅鑄件的全盛期,工藝上已達(dá)到相當(dāng)高的水平。常見的鑄造方法有哪些呢?又各有怎樣的優(yōu)缺點呢?
1.普通砂型鑄造
制造砂型的基本原材料是鑄造砂和型砂粘結(jié)劑。最常用的鑄造砂是硅質(zhì)砂,硅砂的高溫性能不能滿足使用要求時則使用鋯英砂、鉻鐵礦砂、剛玉砂等特種砂。應(yīng)用最廣的型砂粘結(jié)劑是粘土,也可采用各種干性油或半干性油、水溶性硅酸鹽或磷酸鹽和各種合成樹脂作型砂粘結(jié)劑。砂型鑄造中所用的外砂型按型砂所用的粘結(jié)劑及其建立強度的方式不同分為粘土濕砂型、粘土干砂型和化學(xué)硬化砂型3種。
優(yōu)點:
粘土的資源豐富、價格便宜。使用過的粘土濕砂經(jīng)適當(dāng)?shù)纳疤幚砗螅^大部分均可回收再用;制造鑄型的周期短、工效高;混好的型砂可使用的時間長;適應(yīng)性很廣。小件、大件,簡單件、復(fù)雜件,單件、大批量都可采用;
缺點及局限性:
因為每個砂質(zhì)鑄型只能澆注一次,獲得鑄件后鑄型即損壞,必須重新造型,所以砂型鑄造的生產(chǎn)效率較低;鑄型的剛度不高,鑄件的尺寸精度較差;鑄件易于產(chǎn)生沖砂、夾砂、氣孔等缺陷。
2.熔模鑄造
用蠟料做模樣時,熔模鑄造又稱"失蠟鑄造"。熔模鑄造通常是指在易熔材料制成模樣,在模樣表面包覆若干層耐火材料制成型殼,再將模樣熔化排出型殼,從而獲得無分型面的鑄型,經(jīng)高溫焙燒后即可填砂澆注的鑄造方案。由于模樣廣泛采用蠟質(zhì)材料來制造,故常將熔模鑄造稱為“失蠟鑄造”?捎萌勰hT造法生產(chǎn)的合金種類有碳素鋼、合金鋼、耐熱合金、不銹鋼、精密合金、永磁合金、軸承合金、銅合金、鋁合金、鈦合金和球墨鑄鐵等。
優(yōu)點:
尺寸精度較高。一般可達(dá)CT4-6(砂型鑄造為CT10~13,壓鑄為CT5~7);可以提高金屬材料的利用率。熔模鑄造能顯著減少產(chǎn)品的成形表面和配合表面的加工量,節(jié)省加工臺時和刃具材料的消耗;能最大限度地提高毛坯與零件之間的相似程度,為零件的結(jié)構(gòu)設(shè)計帶來很大方便。鑄造形狀復(fù)雜的鑄件熔模鑄造能鑄出形狀十分復(fù)雜的鑄件,也能鑄造壁厚為0.5mm、重量小至1g的鑄件,還可以鑄造組合的、整體的鑄件;不受合金材料的限制。熔模鑄造法可以鑄造碳鋼、合金鋼、球墨鑄鐵、銅合金和鋁合金鑄件,還可以鑄造高溫合金、鎂合金、鈦合金以及貴金屬等材料的鑄件。對于難以鍛造、焊接和切削加工的合金材料,特別適宜于用精鑄方法鑄造;生產(chǎn)靈活性高、適應(yīng)性強熔模鑄造既適用于大批量生產(chǎn),也適用小批量生產(chǎn)甚至單件生產(chǎn)。
缺點及局限性:
鑄件尺寸不能太大工藝過程復(fù)雜鑄件冷卻速度慢。熔模鑄造在所有毛坯成形方法中,工藝最復(fù)雜,鑄件成本也很高,但是如果產(chǎn)品選擇得當(dāng),零件設(shè)計合理,高昂的鑄造成本由于減少切削加工、裝配和節(jié)約金屬材料等方面而得到補償,則熔模鑄造具有良好的經(jīng)濟性。
3.壓鑄
壓鑄工藝原理是利用高壓將金屬液高速壓入一精密金屬模具型腔內(nèi),金屬液在壓力作用下冷卻凝固而形成鑄件。冷、熱室壓鑄是壓鑄工藝的兩種基本方式。冷室壓鑄中金屬液由手工或自動澆注裝置澆入壓室內(nèi),然后壓射沖頭前進,將金屬液壓入型腔。在熱室壓鑄工藝中,壓室垂直于坩堝內(nèi),金屬液通過壓室上的進料口自動流入壓室。壓射沖頭向下運動,推動金屬液通過鵝頸管進入型腔。金屬液凝固后,壓鑄模具打開,取出鑄件,完成一個壓鑄循環(huán)。
優(yōu)點:
產(chǎn)品質(zhì)量好。鑄件尺寸精度高,一般相當(dāng)于6~7級,甚至可達(dá)4級;表面光潔度好,一般相當(dāng)于5~8級;強度和硬度較高,強度一般比砂型鑄造提高25~30%,但延伸率降低約70%;尺寸穩(wěn)定,互換性好;可壓鑄薄壁復(fù)雜的鑄件;生產(chǎn)效率高,例如國產(chǎn)JⅢ3型臥式冷空壓鑄機平均八小時可壓鑄600~700次,小型熱室壓鑄機平均每八小時可壓鑄3000~7000次;壓鑄型壽命長,一付壓鑄型,壓鑄鐘合金,壽命可達(dá)幾十萬次,甚至上百萬次;易實現(xiàn)機械化和自動化;經(jīng)濟效果優(yōu)良。由于壓鑄件尺寸精確,表泛光潔等優(yōu)點。一般不再進行機械加工而直接使用,或加工量很小,所以既提高了金屬利用率,又減少了大量的加工設(shè)備和工時;鑄件價格便易;可以采用組合壓鑄以其他金屬或非金屬材料。既節(jié)省裝配工時又節(jié)省金屬。
缺點及局限性:
壓鑄時由于液態(tài)金屬充填型腔速度高,流態(tài)不穩(wěn)定,故采用一般壓鑄法,鑄件易產(chǎn)生氣孔,不能進行熱處理;對內(nèi)凹復(fù)雜的鑄件,壓鑄較為困難;高熔點合金(如銅,黑色金屬),壓鑄型壽命較低;不宜小批量生產(chǎn),其主要原因是壓鑄型制造成本高,壓鑄機生產(chǎn)效率高,小批量生產(chǎn)不經(jīng)濟。
4.金屬型鑄造
又稱硬模鑄造,它是將液體金屬澆入金屬鑄型,以獲得鑄件的一種鑄造方法。鑄型是用金屬制成,可以反復(fù)使用多次(幾百次到幾千次),又叫永久型鑄造。一般的,金屬型用鑄鐵和鑄鋼制成。鑄件的內(nèi)腔既可用金屬芯、也可用砂芯。金屬型的結(jié)構(gòu)有多種,如水平分型、重直分型及復(fù)合分型。其中垂直分型便于開設(shè)內(nèi)澆口和取出鑄件;水平分型多用來生產(chǎn)薄壁輪狀鑄件;復(fù)合分型的上半型是由垂直分型的兩半型采用鉸鏈連結(jié)而成,下半型為固定不動的水平底板,主要應(yīng)用于較復(fù)雜鑄件的鑄造。
優(yōu)點:
復(fù)用性好,可“一型多鑄”,節(jié)省了造型材料和造型工時。由于金屬型對鑄件的冷卻能力強,使鑄件的組織致密、機械性能高。鑄件的尺寸精度高,公差等級為IT12~I(xiàn)T14;表面粗糙度較低,Ra為6.3m。金屬型鑄造不用砂或用砂少,改善了勞動條件。
缺點及局限性:
金屬型的制造成本高、周期長、工藝要求嚴(yán)格,不適用于單件小批量鑄件的生產(chǎn),主要適用于有色合金鑄件的大批量生產(chǎn),如飛機、汽車、內(nèi)燃機、摩托車等用的鋁活塞、汽缸體、汽缸蓋、油泵殼體及銅合金的軸瓦、軸套等。對黑色合金鑄件,也只限于形狀較簡單的中、小鑄件。
5.低壓鑄造
低壓鑄造是指使液體金屬在較低壓力(0.02~0.06MPa)作用下充填鑄型,并在壓力下結(jié)晶以形成鑄件的方法。把熔煉好的金屬液倒入保溫坩堝,裝上密封蓋,升液導(dǎo)管使金屬液與鑄型相通,鎖緊鑄型,緩慢地向坩堝爐內(nèi)通入干燥的壓縮空氣,金屬液受氣體壓力的作用,由下而上沿著升液管和澆注系統(tǒng)充滿型腔,并在壓力下結(jié)晶,鑄件成型后撤去坩堝內(nèi)的壓力,升液管內(nèi)的金屬液降回到坩堝內(nèi)金屬液面。
開啟鑄型,取出鑄件。
優(yōu)點:
澆注時金屬液的上升速度和結(jié)晶壓力可以調(diào)節(jié),故可適用于各種不同鑄型(如金屬型、砂型等),鑄造各種合金及各種大小的鑄件;采用底注式充型,金屬液充型平穩(wěn),無飛濺現(xiàn)象,可避免卷入氣體及對型壁和型芯的沖刷,鑄件的氣孔、夾渣等缺陷少,提高了鑄件的合格率;鑄件在壓力下結(jié)晶,鑄件組織致密、輪廓清晰、表面光潔,力學(xué)性能較高,對于大薄壁件的鑄造尤為有利;省去補縮冒口,金屬利用率提高到90%~98%;勞動強度低,勞動條件好,設(shè)備簡易,易實現(xiàn)機械化和自動化。
缺點及局限性:
升液管壽命短,且在保溫過程中金屬液易氧化和產(chǎn)生夾渣。主要用來鑄造一些質(zhì)量要求高的鋁合金和鎂合金鑄件,如氣缸體、缸蓋、曲軸箱和高速內(nèi)燃機的鋁活塞等薄壁件。
6.離心鑄造
離心鑄造是將金屬液澆入旋轉(zhuǎn)的鑄型中,在離心力作用下填充鑄型而凝固成形的一種鑄造方法。根據(jù)鑄型旋轉(zhuǎn)軸線在空間的位置,常見的離心鑄造可分為兩種:臥式離心鑄造:鑄型的旋轉(zhuǎn)軸線處于水平狀態(tài)或與水平線夾角很小(<4°)時的離心鑄造。立式離心鑄造:鑄型的旋轉(zhuǎn)軸線處于垂直狀態(tài)時的離心鑄造稱為立式離心鑄造。鑄型旋轉(zhuǎn)軸與水平線和垂直線都夾有較大角度的離心鑄造稱為傾斜軸離心鑄造,但應(yīng)用很少。
優(yōu)點:
用離心鑄造生產(chǎn)空心旋轉(zhuǎn)體鑄件時,可省去型芯、澆注系統(tǒng)和冒口;由于旋轉(zhuǎn)時液體金屬在所產(chǎn)生的離心力作用下,密度大的金屬被推往外壁,而密度小的氣體、熔渣向自由表面移動,形成自外向內(nèi)的定向凝固,因此補縮條件好,鑄件組織致密,力學(xué)性能好;便于澆注“雙金屬”軸套和軸瓦,如在鋼套內(nèi)鑲鑄一薄層銅襯套,可節(jié)省價格較貴的銅料;充型能力好;消除和減少澆注系統(tǒng)和冒口方面的消耗。
缺點及局限性:
鑄件內(nèi)自由表面粗糙,尺寸誤差大,品質(zhì)差;不適用于密度偏析大的合金(如鉛青銅)及鋁、鎂等合金
1.普通砂型鑄造
制造砂型的基本原材料是鑄造砂和型砂粘結(jié)劑。最常用的鑄造砂是硅質(zhì)砂,硅砂的高溫性能不能滿足使用要求時則使用鋯英砂、鉻鐵礦砂、剛玉砂等特種砂。應(yīng)用最廣的型砂粘結(jié)劑是粘土,也可采用各種干性油或半干性油、水溶性硅酸鹽或磷酸鹽和各種合成樹脂作型砂粘結(jié)劑。砂型鑄造中所用的外砂型按型砂所用的粘結(jié)劑及其建立強度的方式不同分為粘土濕砂型、粘土干砂型和化學(xué)硬化砂型3種。
優(yōu)點:
粘土的資源豐富、價格便宜。使用過的粘土濕砂經(jīng)適當(dāng)?shù)纳疤幚砗螅^大部分均可回收再用;制造鑄型的周期短、工效高;混好的型砂可使用的時間長;適應(yīng)性很廣。小件、大件,簡單件、復(fù)雜件,單件、大批量都可采用;
缺點及局限性:
因為每個砂質(zhì)鑄型只能澆注一次,獲得鑄件后鑄型即損壞,必須重新造型,所以砂型鑄造的生產(chǎn)效率較低;鑄型的剛度不高,鑄件的尺寸精度較差;鑄件易于產(chǎn)生沖砂、夾砂、氣孔等缺陷。
2.熔模鑄造
用蠟料做模樣時,熔模鑄造又稱"失蠟鑄造"。熔模鑄造通常是指在易熔材料制成模樣,在模樣表面包覆若干層耐火材料制成型殼,再將模樣熔化排出型殼,從而獲得無分型面的鑄型,經(jīng)高溫焙燒后即可填砂澆注的鑄造方案。由于模樣廣泛采用蠟質(zhì)材料來制造,故常將熔模鑄造稱為“失蠟鑄造”?捎萌勰hT造法生產(chǎn)的合金種類有碳素鋼、合金鋼、耐熱合金、不銹鋼、精密合金、永磁合金、軸承合金、銅合金、鋁合金、鈦合金和球墨鑄鐵等。
優(yōu)點:
尺寸精度較高。一般可達(dá)CT4-6(砂型鑄造為CT10~13,壓鑄為CT5~7);可以提高金屬材料的利用率。熔模鑄造能顯著減少產(chǎn)品的成形表面和配合表面的加工量,節(jié)省加工臺時和刃具材料的消耗;能最大限度地提高毛坯與零件之間的相似程度,為零件的結(jié)構(gòu)設(shè)計帶來很大方便。鑄造形狀復(fù)雜的鑄件熔模鑄造能鑄出形狀十分復(fù)雜的鑄件,也能鑄造壁厚為0.5mm、重量小至1g的鑄件,還可以鑄造組合的、整體的鑄件;不受合金材料的限制。熔模鑄造法可以鑄造碳鋼、合金鋼、球墨鑄鐵、銅合金和鋁合金鑄件,還可以鑄造高溫合金、鎂合金、鈦合金以及貴金屬等材料的鑄件。對于難以鍛造、焊接和切削加工的合金材料,特別適宜于用精鑄方法鑄造;生產(chǎn)靈活性高、適應(yīng)性強熔模鑄造既適用于大批量生產(chǎn),也適用小批量生產(chǎn)甚至單件生產(chǎn)。
缺點及局限性:
鑄件尺寸不能太大工藝過程復(fù)雜鑄件冷卻速度慢。熔模鑄造在所有毛坯成形方法中,工藝最復(fù)雜,鑄件成本也很高,但是如果產(chǎn)品選擇得當(dāng),零件設(shè)計合理,高昂的鑄造成本由于減少切削加工、裝配和節(jié)約金屬材料等方面而得到補償,則熔模鑄造具有良好的經(jīng)濟性。
3.壓鑄
壓鑄工藝原理是利用高壓將金屬液高速壓入一精密金屬模具型腔內(nèi),金屬液在壓力作用下冷卻凝固而形成鑄件。冷、熱室壓鑄是壓鑄工藝的兩種基本方式。冷室壓鑄中金屬液由手工或自動澆注裝置澆入壓室內(nèi),然后壓射沖頭前進,將金屬液壓入型腔。在熱室壓鑄工藝中,壓室垂直于坩堝內(nèi),金屬液通過壓室上的進料口自動流入壓室。壓射沖頭向下運動,推動金屬液通過鵝頸管進入型腔。金屬液凝固后,壓鑄模具打開,取出鑄件,完成一個壓鑄循環(huán)。
優(yōu)點:
產(chǎn)品質(zhì)量好。鑄件尺寸精度高,一般相當(dāng)于6~7級,甚至可達(dá)4級;表面光潔度好,一般相當(dāng)于5~8級;強度和硬度較高,強度一般比砂型鑄造提高25~30%,但延伸率降低約70%;尺寸穩(wěn)定,互換性好;可壓鑄薄壁復(fù)雜的鑄件;生產(chǎn)效率高,例如國產(chǎn)JⅢ3型臥式冷空壓鑄機平均八小時可壓鑄600~700次,小型熱室壓鑄機平均每八小時可壓鑄3000~7000次;壓鑄型壽命長,一付壓鑄型,壓鑄鐘合金,壽命可達(dá)幾十萬次,甚至上百萬次;易實現(xiàn)機械化和自動化;經(jīng)濟效果優(yōu)良。由于壓鑄件尺寸精確,表泛光潔等優(yōu)點。一般不再進行機械加工而直接使用,或加工量很小,所以既提高了金屬利用率,又減少了大量的加工設(shè)備和工時;鑄件價格便易;可以采用組合壓鑄以其他金屬或非金屬材料。既節(jié)省裝配工時又節(jié)省金屬。
缺點及局限性:
壓鑄時由于液態(tài)金屬充填型腔速度高,流態(tài)不穩(wěn)定,故采用一般壓鑄法,鑄件易產(chǎn)生氣孔,不能進行熱處理;對內(nèi)凹復(fù)雜的鑄件,壓鑄較為困難;高熔點合金(如銅,黑色金屬),壓鑄型壽命較低;不宜小批量生產(chǎn),其主要原因是壓鑄型制造成本高,壓鑄機生產(chǎn)效率高,小批量生產(chǎn)不經(jīng)濟。
4.金屬型鑄造
又稱硬模鑄造,它是將液體金屬澆入金屬鑄型,以獲得鑄件的一種鑄造方法。鑄型是用金屬制成,可以反復(fù)使用多次(幾百次到幾千次),又叫永久型鑄造。一般的,金屬型用鑄鐵和鑄鋼制成。鑄件的內(nèi)腔既可用金屬芯、也可用砂芯。金屬型的結(jié)構(gòu)有多種,如水平分型、重直分型及復(fù)合分型。其中垂直分型便于開設(shè)內(nèi)澆口和取出鑄件;水平分型多用來生產(chǎn)薄壁輪狀鑄件;復(fù)合分型的上半型是由垂直分型的兩半型采用鉸鏈連結(jié)而成,下半型為固定不動的水平底板,主要應(yīng)用于較復(fù)雜鑄件的鑄造。
優(yōu)點:
復(fù)用性好,可“一型多鑄”,節(jié)省了造型材料和造型工時。由于金屬型對鑄件的冷卻能力強,使鑄件的組織致密、機械性能高。鑄件的尺寸精度高,公差等級為IT12~I(xiàn)T14;表面粗糙度較低,Ra為6.3m。金屬型鑄造不用砂或用砂少,改善了勞動條件。
缺點及局限性:
金屬型的制造成本高、周期長、工藝要求嚴(yán)格,不適用于單件小批量鑄件的生產(chǎn),主要適用于有色合金鑄件的大批量生產(chǎn),如飛機、汽車、內(nèi)燃機、摩托車等用的鋁活塞、汽缸體、汽缸蓋、油泵殼體及銅合金的軸瓦、軸套等。對黑色合金鑄件,也只限于形狀較簡單的中、小鑄件。
5.低壓鑄造
低壓鑄造是指使液體金屬在較低壓力(0.02~0.06MPa)作用下充填鑄型,并在壓力下結(jié)晶以形成鑄件的方法。把熔煉好的金屬液倒入保溫坩堝,裝上密封蓋,升液導(dǎo)管使金屬液與鑄型相通,鎖緊鑄型,緩慢地向坩堝爐內(nèi)通入干燥的壓縮空氣,金屬液受氣體壓力的作用,由下而上沿著升液管和澆注系統(tǒng)充滿型腔,并在壓力下結(jié)晶,鑄件成型后撤去坩堝內(nèi)的壓力,升液管內(nèi)的金屬液降回到坩堝內(nèi)金屬液面。
開啟鑄型,取出鑄件。
優(yōu)點:
澆注時金屬液的上升速度和結(jié)晶壓力可以調(diào)節(jié),故可適用于各種不同鑄型(如金屬型、砂型等),鑄造各種合金及各種大小的鑄件;采用底注式充型,金屬液充型平穩(wěn),無飛濺現(xiàn)象,可避免卷入氣體及對型壁和型芯的沖刷,鑄件的氣孔、夾渣等缺陷少,提高了鑄件的合格率;鑄件在壓力下結(jié)晶,鑄件組織致密、輪廓清晰、表面光潔,力學(xué)性能較高,對于大薄壁件的鑄造尤為有利;省去補縮冒口,金屬利用率提高到90%~98%;勞動強度低,勞動條件好,設(shè)備簡易,易實現(xiàn)機械化和自動化。
缺點及局限性:
升液管壽命短,且在保溫過程中金屬液易氧化和產(chǎn)生夾渣。主要用來鑄造一些質(zhì)量要求高的鋁合金和鎂合金鑄件,如氣缸體、缸蓋、曲軸箱和高速內(nèi)燃機的鋁活塞等薄壁件。
6.離心鑄造
離心鑄造是將金屬液澆入旋轉(zhuǎn)的鑄型中,在離心力作用下填充鑄型而凝固成形的一種鑄造方法。根據(jù)鑄型旋轉(zhuǎn)軸線在空間的位置,常見的離心鑄造可分為兩種:臥式離心鑄造:鑄型的旋轉(zhuǎn)軸線處于水平狀態(tài)或與水平線夾角很小(<4°)時的離心鑄造。立式離心鑄造:鑄型的旋轉(zhuǎn)軸線處于垂直狀態(tài)時的離心鑄造稱為立式離心鑄造。鑄型旋轉(zhuǎn)軸與水平線和垂直線都夾有較大角度的離心鑄造稱為傾斜軸離心鑄造,但應(yīng)用很少。
優(yōu)點:
用離心鑄造生產(chǎn)空心旋轉(zhuǎn)體鑄件時,可省去型芯、澆注系統(tǒng)和冒口;由于旋轉(zhuǎn)時液體金屬在所產(chǎn)生的離心力作用下,密度大的金屬被推往外壁,而密度小的氣體、熔渣向自由表面移動,形成自外向內(nèi)的定向凝固,因此補縮條件好,鑄件組織致密,力學(xué)性能好;便于澆注“雙金屬”軸套和軸瓦,如在鋼套內(nèi)鑲鑄一薄層銅襯套,可節(jié)省價格較貴的銅料;充型能力好;消除和減少澆注系統(tǒng)和冒口方面的消耗。
缺點及局限性:
鑄件內(nèi)自由表面粗糙,尺寸誤差大,品質(zhì)差;不適用于密度偏析大的合金(如鉛青銅)及鋁、鎂等合金
上一條:雙端面磨床加工工件時的注意事項
相關(guān)標(biāo)簽:雙端面磨床,瓦型磨床,振動送料器,四端面磨床,通過式雙端面磨床相關(guān)新聞
- 2024-12-20 雙端面磨床加工大小頭不等厚連桿
- 2024-12-20 數(shù)控雙端面磨床自動檢測
- 2024-07-31 雙端面磨床正確安裝方法?
- 2024-07-31 什么是雙端面磨床?
- 2024-07-31 雙端面磨床平行差大怎么調(diào)整
- 2024-04-20 雙端面磨床加工大小頭不等厚連桿